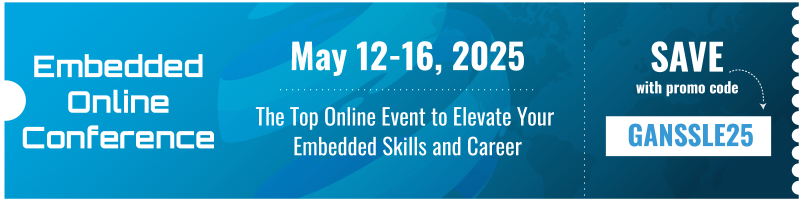
|
|
||||
You may redistribute this newsletter for noncommercial purposes. For commercial use contact jack@ganssle.com. |
||||
Contents | ||||
Editor's Notes | ||||
|
||||
Give your team the tools they need to operate at a measurably world-class level, producing code with far fewer bugs in less time. This is what my one-day Better Firmware Faster seminar is all about. It's fast-paced, fun, and uniquely covers the issues faced by embedded developers. Information here shows how your team can benefit by having this seminar presented at your facility. Follow @jack_ganssle I'm now on Twitter. According to a recent survey, there are 10 types of people in this world: those who understand binary and those who don't. As you are one of the former and also experienced in the ways of embedding, won't you please participate in a quick online survey that the Barr Group and I are running to learn about trends in our industry? The survey is here. Figure on 5 minutes, after which you will be automatically entered into a drawing to win one of two Saleae Logic 8 USB logic analyzers or three $25 Amazon gift cards. |
||||
Quotes and Thoughts | ||||
"We live in a society exquisitely dependent on science and technology, in which hardly anyone knows anything about science and technology. This is a clear prescription for disaster." - Carl Sagan |
||||
Tools and Tips | ||||
Please submit clever ideas or thoughts about tools, techniques and resources you love or hate. Here are the tool reviews submitted in the past. Clyde Shappee had some thoughts about Kicad:
|
||||
Freebies and Discounts | ||||
This month I'm giving away a copy of Gary Stringham's excellent Hardware/Firmware Interface Design. The contest will close at the end of January, 2016. It's just a matter of filling out your email address. As always, that will be used only for the giveaway, and nothing else. Enter via this link. |
||||
Fancy IDEs? | ||||
Charles Manning had some thoughts about fancy IDEs:
Over the years I've heard from many engineers that their development environment wouldn't run on the latest version of Windows. So they stash an old Windows machine in storage in case maintenance is needed. But that's no guarantee; capacitors go bad with age so that old machine may not run. Some companies are required to support a product for 30 years (notably in the railroad industry). 30 years ago the current version of Windows was 1.0. Linux didn't exist. The Mac was only two years old and used floppies, a 68000 processor, and a long-defunct OS. Just this week I heard from a developer who needed to get files off an 8" floppy disk drive! In the 1980s I got a contract to change some code, which had been developed on a paper-tape-based system. There wasn't enough of a budget to port it to a newer environment, so I delivered the updated code on paper tape. We may have a new problem looming - solid state disks. Archive a system for anticipated maintenance use a decade or more hence, and the SSD may drop bits since flash memory has a limited life. For example, Spansion's S34ML04G1 device has a ten year (typical; no minimum is rated) data retention period. Long-term support in an age of constant technical revolution is an enormous problem. |
||||
Choosing EDA Tools | ||||
Andrew Retallack wrote:
|
||||
PCB Software | ||||
Paul Carpenter has some thoughts about PCB software:
|
||||
Jobs! | ||||
Let me know if you’re hiring embedded engineers. No recruiters please, and I reserve the right to edit ads to fit the format and intents of this newsletter. Please keep it to 100 words. There is no charge for a job ad. |
||||
Joke For The Week | ||||
Note: These jokes are archived at www.ganssle.com/jokes.htm. Q: "Whats the object-oriented way to become wealthy?" A: Inheritance |
||||
Advertise With Us | ||||
Advertise in The Embedded Muse! Over 25,000 embedded developers get this twice-monthly publication. . |
||||
About The Embedded Muse | ||||
The Embedded Muse is Jack Ganssle's newsletter. Send complaints, comments, and contributions to me at jack@ganssle.com. The Embedded Muse is supported by The Ganssle Group, whose mission is to help embedded folks get better products to market faster. |