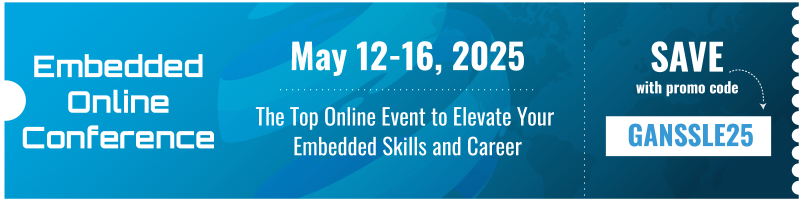
Leaks and Drains, Take 2
Summary: Every nA counts in ultra-low powered MCU circuits. What about PCB contaminants?
In the last couple of years a number of MCUs have become available that have astonishingly-low sleep currents, sometimes in the tens of nanoamps, making it possible to build systems that run for years from a single coin cell battery.
In a recent article (http://www.embedded.com/electronics-blogs/break-points/4399090/Leaks-and-Drains) I mentioned that one must consider leakages on the PCB due to contamination. Finger oils and other impurities might drain far more nanoamps than that required by the microcontroller.
Turns out, I was wrong.
A lot of on-line pundits bloviate that the leakage problem is a big factor; experience shows that the more an Internet poster asserts that X is an indisputable fact, the more likely it's not. (A century and a half ago, Charles Darwin noted that "ignorance more frequently begets confidence than does knowledge.") This is engineering, not speculation, so I decided to run some experiments to see how significant these leaks are in a digital circuit. But how to do so? Clearly, to get meaningful data one must measure these drains to a resolution much better than the 20 nA (nanoamps) or less some of the MCUs use while sleeping.
One could use a DMM to measure leakage in ohms. Mine only goes to 40 Mohms, which at 3 volts would represent about a 100 nA leak. That's too crude. The uCurrent (http://www.embedded.com/electronics-blogs/break-points/4406380/The--Current) tool can resolve to a single nA, which is probably adequate, but at 1 nA it generates only a single mV, which is pushing the resolution of my DMM pretty hard.
So I built a sample and hold circuit (S&H). A high quality polypropylene 1 æF capacitor feeds a very high impedance op amp follower. Put a component whose properties you want to measure around the cap, charge it up, and watch the discharge curves by reading the op amp.
Sample & Hold circuit to test for very low leakages
I used an LM662 op amp, which has a 2 femtoamp (typical - no max is listed) input bias current. One fA is a miniscule 10-15 amps, a millionth of a billionth of an amp, or about 6000 electrons/second, so its effect on the capacitor is minimal. The amplifier's inputs and the cap's connection are all made in the air. An mbed.org Cortex M3 controller with a 12 bit A/D reads the amplifier periodically, as well as temperature and humidity sensors, and shoots the results to a PC via USB for logging.
Measuring the time constant with a 10 Mohm resistor across the capacitor proved the circuit worked as expected. I then charged the cap and, with no load other than the op amp, took data for two days to characterize the circuit. The results are summarized in the following graph.
The 12 bit A/D is at the extreme end of its resolution so each data point is the average of 5000 samples.
Clearly the voltage is highly dependent on temperature. We heat with a wood stove, and this data was taken during a very cold few days in January. The dips bottomed out in the morning as the house cooled all night; they veered up when I restarted the fire.
My goal was to measure the resolution of the circuit, but the results are very hard to interpret as it's tough to separate out the temperature effect. Has it discharged at all?
The voltage across a capacitor that is discharging over time is:
Where V0 is the initial voltage on the cap and t is the elapsed time. Taking the natural log and rearranging we get:
R is the effective resistance that bleeds charge from the capacitor. Some of that "resistance" is due to the bias current going into the op amp; some is in the cap body itself, and some is from leakage into air.
Ohm's Law converts R to amps. If the voltage decayed by 1 mV this gives 6.6 fA of leakage from all sources. Alternatively, by plugging 10 fA into the equation the voltage would have decayed to 3.228, which would have been very easy to see. So the S&H can resolve better than 10 fA. That's many orders of magnitude lower than any leakage that would concern us in designing a low-power system.
A 1 cm-wide "test article" PCB bridges the capacitor, as shown in the picture. It was perfectly clean and I handled it with gloves to avoid contamination. There's a 0.5mm grove whittled across the board. How much does FR-4 material leak in 30% relative humidity? I have no idea. But the S&H confirmed that it's less than 10 fA.
Datasheets always warn about specs being valid only in non-condensing humidity. How important is that? I boiled some water and collected the condensate to emulate the sort of moisture that likely makes up water vapor in the air, and bridged the test article's insulating gap with a 2 mm diameter drop. Just over 1 æA flowed, in line with figures available on-line. Conductivity is measured in units of ohm-meters, so there could be a lot of æA flowing in a real PCB with more surface area under water.
Despite extensive searches I couldn't find any useful data about how the conductivity of a PCB is affected by humidity. Alas, I don't have convenient access to an environmental chamber so ran some very crude experiments.
I covered the test article and humidity sensor with a plastic coffee can with a hose protruding from the bottom. Taking data in real time (with humidity and voltage readings displayed on the PC) I huffed and puffed into the hose. At 70% relative humidity the test article's leakage went from under 10 fA to 13 pA, a jump of three orders of magnitude. At 80% (the highest I was able to achieve) that went to 20 pA. Now, this is over a 1 cm long gap, so a better metric is 20 pA/cm. A board with 50 cm of track would experience about 1 ?A of leakage, enough to eat almost half of a CR2032 battery's 10 year power budget of 2.5 ?A.
There are two mechanisms for leakage due to humidity. The first is through the moist air that separates two tracks or terminals. The second is via adsorption of water molecules on the surface of the PCB. Other contaminates like dirt that might have a very low conductivity can adsorb water molecules and reduce the board's resistance. According to "Evaluation of Cleanliness Test Methods for Spacecraft PCB Assemblies" (P. E. Tegehall and B. D. Dunn, ESA STM-275, October 2006) a water film just 20 molecules thick will have a conductivity that is only an order of magnitude lower than that of bulk water.
What about contamination? Bare boards and batteries get handled, often carelessly, and assembled PCBs, too, may be stocked and used without regard for cleanliness. A common concern is leakage due to finger oils. Lots of on-line pedants complain that this is a very significant problem. But hard data is scarce.
I grabbed a bottle of my wife's Jergens Dry Skin Moisturizer, Original Scent, and spread the thinnest layer I could on the test article insuring the entire 1 cm long gap between copper foils was bridged. The leakage was too much to measure with the S&H. But 24 hours later, after the volatiles evaporated, it was down to 180 pA. After another day the leakage hadn't changed. That's 0.18 nA, not much, but is over a short 1 cm length, and could add up with lots of contaminated PCB tracks.
But this is a really contrived experiment.
After cleaning the board with isopropyl alcohol the leakage was 2 pA, the better part of three orders of magnitude worse than when I tested the fresh, uncontaminated board. More cleaning didn't help. The Moisturizer had effected some change to the PCB. Happily, 2 pA is a very small value, though it could be disastrous to some analog circuits.
Next came the finger oil test using both lovely soft female fingers which an hour earlier had been gooped up with the Jergens, as well as nasty crackled Jergens-free male fingers. We touched the test article gently, rubbed some, then smeared furiously. In no case did the leakage exceed 8 pA. Now, that's enough to cause the S&H's output to droop by more than 50 mV in 20 seconds, devastating in a sensitive analog sample and hold circuit. But it's not enough to have any measurable affect on battery life.
Since containments can increase the adsorption of water molecules I exposed the finger-oily test article to 80% relative humidity. The numbers rocketed to 65 pA, three times the humidity result with a clean board. Again, 65 pA is nothing, but multiply your track lengths by the 1 cm long test article used in this experiment.
Could leakage come from salts left behind from perspiration? I mixed up a solution of warm water and salt, supersaturating the solution to the point where the water could hold no more salt, and completely coated the 1 cm gap in the test article. Wet, the leakage was unsurprisingly too huge to measure with this circuit. But after the water dried, it dropped to under 50 fA at 30% ambient relative humidity.
That's with dry salt. Subjecting the test article to 50% relative humidity caused the leakage to jump to 2 æA.
This is also very contrived test. It's hard to believe that handling a board would leave so much salt behind (as confirmed by my finger-oil experiments).
Using a fresh test article, I tested several kinds of rosin, first soldering while taking care to ensure the rosin smeared across the gap in the copper foil, and later just gooping bulk rosin across it. The worst leakage was 2 pA. Adding 80% humidity simply boosted the number to 20 pA, the same result for a clean test article.
Interestingly, careful cleaning with isopropyl alcohol boosted the drain to 32 pA over the 1 cm gap length. Recleaning even more carefully got that down to 4 pA. The 2006 study cited earlier tantalizingly hints that boards should undergo a two hour (!) bath in an ultrasonic cleaner.
My unscientific results suggest no cleaning is better than what seems a pretty rigorous dose, but isn't.
What about solder mask? I reran the salt water experiment on a PCB whose traces were covered by a solder mask. Even sopping wet, the leakage was under 10 fA. The finger oil experiments, too, gave leakages too low to measure. Ditto for smearing Jergens on the board. The solder mask seems to be a nearly-perfect insulator, though of course there will be no mask around solder joints.
To summarize, assuming no sensitive analog circuits, the experiments showed: Finger oils are not a big deal. Humidity matters if there's a lot of exposed track and the humidity is very high for a long time. Condensing water is bad. Cleaning is hard, and may cause even worse problems. Solder mask solves essentially all of the leakage problems.
The takeaway is that the usual practice of putting a layer of solder mask on a PCB eliminates leakage problems related to battery-powered MCUs. Don't worry about assemblers mishandling the board or the battery. There will be leakage around exposed pads, but outside of extreme environments that should have no noticeable effect on battery life.
(Thanks to Alan Steines for his suggestions and input on these experiments.)
Published July 12, 2013