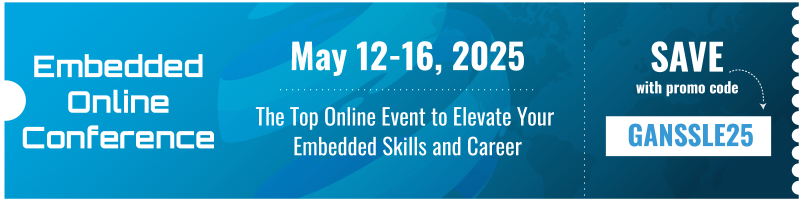
Tool Quest
Decent tools make us more productive. If your time has any value, don't skimpt on them!Published in EDN, May 1996
By Jack Ganssle
Years ago I worked for a small, 100 person outfit that experienced a wealth of financial difficulties. Half of the phone calls were from angry creditors. The bank was perpetually on the brink of closing us down. Still, our small engineering group always had a reasonable set of tools. Good scopes then cost upwards of $10,000, a lot of money in 1975 dollars. We even managed to get one of Intel's first microprocessor development systems. Though we engineers had to cajole and plead with management for the tools, we did get them, and developed an expectation that we'd always have access to whatever the job needed.
Then I started consulting.
Suddenly, those wonderful tools we had so long taken for granted were no long available. My partner and I shared an old Tektronix 545 scope (that used vacuum tubes - you know, those glass-shelled things with filaments and high voltages). We scraped up enough money to build an emulator - such as it was - from mail ordered Multibus boards. A $400 CRT terminal and daisy wheel printer were all we could afford in the way of new capital equipment.
We learned all sorts of ways to extract information from systems, pouring loads of time into projects instead of cash.
Then I met a fellow whose high school kid had a lab of sorts in his home. He had a new Tektronix scope! I was flabbergasted. Though the unit wasn't top-of-the-line, it sure beat the antique I was saddled with.
A few discrete questions turned up the fact that he rented the scope, for a lousy $50 a month. Somehow it had never occurred to me that there were options other than coming up with thousands in cash. This mere kid showed me that the quest to obtain the right tools is a problem, one like any other problem we run into in engineering and life, one that takes a bit of creative energy to solve.
Coming up with the Bucks
Ain't America grand? Easy credit, available to practically any warm body, means we can satisfy practically any whim... as far too many of us do until the inevitable day of reckoning comes.
Look at the computers advertised in any PC magazine. Every ad has a caption giving the low, low monthly payment they'll require... a payment that is surprisingly low. If your business has any income at all, then the hundred a month or so for a high-end machine is a pittance.
Test equipment vendors all offer similar plans. You'd be surprised how low the monthly payments on a scope are, when spread over 3 to 5 years.
Most companies will bend over backwards to finance your purchase. Those that have no in-house financing ability work with third party financial outfits. Test equipment companies really want you to have their latest widget, and will do practically anything to help you purchase it.
Renting is a traditional means to get access to equipment for short periods of time. However, unless you're quite convinced that the project will end as planned, be wary of rentals. Few short term projects fail to increase in scope and duration. Since rentals generally cost around 10% of the unit's purchase price per month, once the project slips more than a quarter, you may have been better off buying than renting. Leases are the most attractive way to get equipment you can't afford to buy outright. A lease with buyout clause is nothing more than a financed purchase. It may have certain tax benefits as well, though this part of the law changes constantly.
Even for a single scope you can get leases amortized over practically any amount of time. Three years is a common period. The monthly payment will be something like 3% of the unit's purchase price per month. A $5,000 logic analyzer will set you back around $200 per month. For less than your car payment you can get a nice scope and logic analyzer. Unlike the car, neither will wear before the payments are up.
Sometimes it makes sense just to purchase gear outright, especially since the IRS permits you to expense $17,500 of "capital" equipment per year. When cash is tight consider getting used, refurbished test equipment. A number of outfits sell reconditioned gear for around 50 cents on the dollar. Good test equipment lasts almost forever.
Always be on the lookout for good deals. The truckload of Dell Pentiums we recently bought came loaded with Microsoft Office... and $29 certificates for upgrades to the Win95 version. Sure beats paying the folks in Redmond half a thousand per machine for the software!
One acquaintance has just a shell of a company, a so-called "virtual corporation" that changes dynamically as business ebbs and flows. He shares an office suite with other like-structured organizations. All are in the digital business, and use a common lab area with shared test equipment. For small outfits this is a neat way to make the dollar go a lot further.
Spend Money to Save
One of the cool things about my current job is that I get to peer into the engineering departments of lots of different companies. It's rather shocking what one sees. The tool engineers use more than anything else is a computer of some sort - now, mostly PCs. Yet probably less than a third of the folks I talk to use even moderately state of the art equipment. 486s are de rigor. The 386 - even SX versions - are far too common.
Two years ago we put top-end 486-66s on all of the engineers' desks. Recently these went to the metaphorical scrap heap, replaced by Pentium-133s loaded with everything.
The wags tell us that money can't buy happiness. Maybe so, but it can surely buy productivity.
The facts: compile times, for our biggest program (150,000 lines of C) went from 30 minutes to 4. Windows help files, previously needing almost 4 hours to build, now complete in 12 minutes. The biggest and klunkiest utilities that were at least annoying in their 10s of seconds of load times now start up in under a second.
These sorts of time savings translate into immediate real productivity improvements.
That $4k/machine is a pittance compared to the salary of an engineer. Too many companies fail to recognize that arming an expensive designer with crummy, slow tools is nothing more than a very efficient way of burning $1000 bills.
(This corporate stinginess extends to other areas as well. Read DeMarco's and Lister's Peopleware: their tests conclude that a private office and some quiet can yield almost a 3-fold improvement in programming productivity. Yet at most large companies armies of engineers live in seas of noisy cubicles. )
It's time we recognized that the true cost of an engineer is includes salary, plus some tool budget amortized of the realistic life of the tools. Though the IRS expects 5 year computer depreciation, two years is more realistic for keeping those salary dollars generating the maximum return.
Even a one-man consulting firm needs the same sort of equipment employed by the richest mega-corporation. A smart consultant uses better gear, as anything that makes him more efficient puts more dollars in his pocket. The problem is paying for it.
Info Overload
You'll do your company a disservice, though, by acquiring decent equipment without the expertise needed to use it effectively. How many folks today understand and use delayed sweep?
Everything we buy - even a lousy $30 watch - comes with a huge instruction manual. It's the bane of the computer age - embedded processors make everything smart, so smart we haven't the time to master any of it. I'm writing this in front of a stereo whose video and tape modes have had me baffled for years. Perhaps I could dig out the manual (from the filing cabinet that overflows with similarly unread manuals), but it's simply not a priority.
We're suffering from information overload. No one has time to become proficient with any of our wonderful gadgets. We use each device's simplest modes, never progressing much beyond the basics. Watch a secretary struggle with any modern word processor. Very few have mastered the art of working with multichapter documents, or are comfortable with grammar checkers or electronic thesauruses.
Explore the boundaries of your tools. Be an expert with those that pay your mortgage, like the scope and logic analyzer. Treat each switch and operating mode as a challenge; dedicate an hour or so a week to mastering its intricacies. The more you know, the more efficiently you'll get your job done.
There are plenty of ways to get the equipment you need to be productive. Some are a bit shady. One acquaintance went from vendor to vendor, getting demo copiers for a week or two at a time, avoiding buying for a couple of years.
Happily, despite what we hear on the evening news, the vast majority of businesses operate very honestly. Pay for what you use, so your customers behave the same way to you.