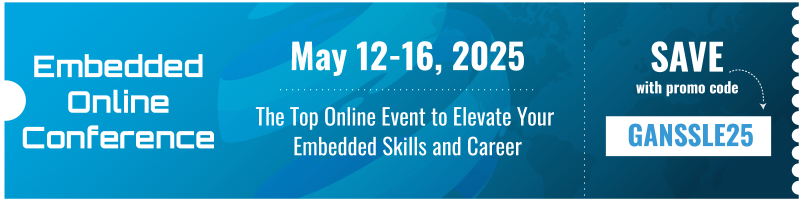
Prototyping with SMT
Using SMT brings in a new set of challenges. It's not as easy as the good 'ole DIP days!
By Jack Ganssle
I pity the poor solitary inventor, working out of the basement on the "next great thing", scarfing parts from surplus catalogs, squeezing the future from a meager budget. Our industry's headlong dash into the future is squeezing these entrepreneurs out of existence.
The price of entry into modern electronics has skyrocketed. No longer can you slap a breadboard together with parts from the local Radio Shack. Without PCB capability high speed digital is impossibly unreliable. Expensive design tools limit the use of FPGAs, PLDs, and the like to corporations only.
Even ten years ago the basement designer had access to pretty much any digital technology. No longer. Skyrocketing complexity brings wonders to the consumer for almost no cost, yet bars all but the well-heeled from the field. There are plenty of analogies: shadetree auto mechanics are fast fading from the scene. My 60-era's VW microbus had all of 5 wires going to its engine. Any amateur could adjust the valves or even replace the pistons and cylinders. Now, a look under the hood of a modern automobile inspires panic, the hundreds of wires and hoses snaking who knows where, with not even a clue where the spark plugs (do they still use spark plugs?) live.
Surface Mount Technology (SMT) is the latest trend that demands special equipment and capabilities. It's fast becoming a necessity in digital circuits. Like other advances, SMT also increases the cost of entry to the use of modern technologies.
I was dragged into SMT kicking and screaming a few years back, afraid of the costs, and concerned about our ability to produce reliable circuits. At the time we had the opportunity and leisure to try a few tentative experiments, creating a few all-SMT boards in a low-risk learning environment. Now nearly all of our designs are surface mount, and all have benefited from our prolonged dance with the new technology.
We're finding that getting parts for even three year old through-hole designs is tough. Memories, in particular, are often more easily available in SMT packages. Emulation Technology and others produce adapters that let you plug JDEC surface mount parts into DIP hole patterns. On older board layouts we've found it convenient to add SMT pads inside of the DIP patterns, giving us the option of using any sort of part.
SMT brings two primary values to a design: the resulting boards are smaller, and the parts are easier to get. Count on many new chips coming out exclusively in surface mount packages.
The downside is the difficulty of using this technology. Production issues are beyond the scope of this article (except for one hint listed at the end). I'm more interested in how we designers construct and troubleshoot prototypes.
Building a Prototype
A soldering guru, based here in Columbia, MD, came by to visit one day, extolling his special expertise at constructing anything. He reeked of hot flux, and his hands were scarred by repeated encounters with soldering irons. "I can plop those .020" pins down with just a fine-point iron" he crowed. As one who drinks too much coffee each morning, I had long since given up the hope of soldering even the coarsest of fine pitch devices, but this fellow seemed to offer a nice solution to creating our prototype boards. We let him have a couple, and sure enough - two days later they were back in the shop with all of the devices firmly attached.
None worked. A careful examination under the microscope revealed a pattern of unsoldered pins - particularly those under J-leaded devices - and almost invisible shorts.
Iterating this experiment with more boards and more assemblers yielded the same general results. With infinite effort it is possible to successfully attach even a 208 pin monster with nothing more than a very hot, very sharp soldering iron. However, when a board has a dozen of these, even the best intentions and finest assembler aren't enough to reliably attach all of the parts. This was but one of a number of failed experiments. In the end we purchased a surface mount soldering station - in our case, the MTR5000 from OK Industries. At more than $7k this is one expensive soldering iron!
The device comes with an array of more or less conventional irons, as well as a hot air pencil used to reflow the solder, and a suction probe used to place components on the board. It's best feature, though, is an elevator-like affair that places the component and solders it at the same time. Human frailties that make manual SMT soldering impossible are bested by this part of the system.
Before placing a part you'll spread solder paste onto the board's pads. Then, with a vacuum holding the component; you lower it onto the board by twisting a knob that brings both the component and a hot-air nozzle into position.
Every package needs a different hot air nozzle, as these surround the component and are precisely engineered to put a lot of heat in exactly the right place, for a very short time. It's kind of neat to watch the solder paste melt and flow around the pins.
With practice this is a very reliable procedure. It's not fast, and is therefore suitable only for prototype or very low volume production. However, a trained assembler can build correct boards pretty much every time.
Practice is essential. This is a manual process requiring a sense of the correct amount of heat and solder paste, and of positioning. We found the practice boards that are available from a number of sources to be worthless, as they don't include fine pitch parts.
At .020" lead pitch, only those engineers and technicians that work with the machine every day can use it well. I, however, am an utter failure, and slink quietly by as these masters do their magic.
We found the TV microscope to be more trouble than it's worth. Some magnification is critical; a regular optical microscope with 10 to 20 power and a wide field of view is ideal. An intense source of light, and abstinence from caffeine are both critical.
Testing and Troubleshooting
A prototype, once assembled, is still a prototype and surely harbors a wealth of problems you the engineer must uncover.
In the good old days of through-hole boards most of us learned that the first step in bringing a product forth was to visually inspect all of the soldering. It's the fastest way to find manufacturing problems. The same lesson holds true with SMT.
Under a bright light, go over each pin with a sharp dental instrument. Techni-Tool offers a variety of these in their catalog, and I have found no better tool for SMT. Perfectly soldered pins will leap out in their perfection; those perhaps less well connected should be tested by gently prying the pin.
Sometimes you can run the tool down a row of pins and listen to the sound. A dull "thunk" is a dead giveaway that something is not right.
SMT pins make a mockery of crude ham-fisted hands. Somehow you've got to get that scope probe on exactly the right one of 132 pins. It's hard to figure out which pin is the right one, and it's even harder to hold a probe in position against that pin.
I use an X-acto knife to make a scratch mark on the PCB near every tenth pin on high density devices. This helps me get on the right pin. And, it cuts down on that infuriating counting! One eyeblink and you've lost position, having to go pack to pin one and start all over.
That same X-acto knife (one of the handiest of SMT tools) is a nice prober for low-speed signals. Clip your scope probe to it and use the ultra-sharp end to get on the right pad.
On higher-speed logic consider using the knife's blade -- without the handle -- as the probe. Alternatively, remove the scope probe's slip-on tip and sharpen the central pin. In my experience these don't stay sharp long... perhaps some fine brand of cutlery will someday market "Ginzu carbon steel scope probes that hold an edge forever!"
It's impossible to connect the average logic analyzer to fine-pitch SMT devices using conventional clips. Invest in a handful of the tiny grabbers produced by several firms. These are like scaled down logic analyzer clips, making one feel rather like a Gulliver in the land of Lilliputians. I get them from Emulation Technology (part number FP-2B). They're frightfully expensive, but provide a good connection to the finest of SMT leads, and are easy to connect.
HP and Tektronix have some innovative probing strategies you should check out as well. This is an area that's evolving rapidly, so read the magazines often.
One Last Comment
And now for that hint about production. First, if you're committed to SMT visit a company that's into the technology in a big way. Look at those monster vapor-phase soldering machines and the careful control of the chemistry of the process.
There's a clear moral: SMT production is a complex operation requiring special expertise. Unless your outfit is large, well funded, and intends to go into mass production, contract out the work. Quality assembly houses dot the landscape; some are hungry, suffering from the downsizing of military contracts. Find a couple of these shops that do a good job, and develop a partnership.
It just doesn't make sense to assume that one organization - yours or anyone else's -- can do everything well.