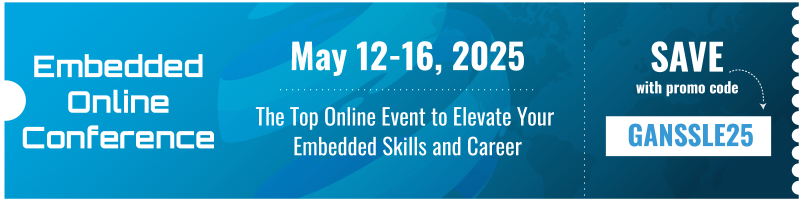
Olden Days
Published in EDN, July, 1996
By Jack Ganssle
After 10PM my house falls silent, the kids long since tucked away, my wife reading or equally lost in dreamland. This is my time, when I get a chance to spend what little energy remains at the close of day on avocations. One of these is amateur astronomy, for which I spend a fair number of these all-too-limited hours pouring over star maps and planning the next observing session.
The other day I stopped at an office supply store to pick up a pair of dividers. No other tool is as useful for extracting stars' celestial position from the charts. Yet somehow these (along with scissors and tape) disappear into the land of the unknown with astonishing rapidity; my queries always answered with a "I don't know" from the youngsters.
This time the store's shelves were bare. The poor substitute was a cheap compass, which immediately puzzled my son. Somehow he assumed it was yet another new marvel of technology like the ones that fill his environment! but where did the battery go?
Computer folks used the same tools as civil engineers. Offices were dominated by the drawing board, a 6 by 3 foot flat panel propped at a "comfortable" angle. Engineers lived in high chairs strangely reminiscent of Dicken's Bob Crachet, hunched over the drawing board with mechanical pencil in hand, creating wonderful silicon inventions using the same paper and lead that writers and philosophers relied on for centuries.
Drafting was a skill all mechanical engineers mastered in college, but for some reason, at the University of Maryland, it was not considered important for electronics guys (guys - all guys. There were virtually no women in the field then). Some engineers were nothing short of gifted artists, creating schematics that filled the paper in a visually pleasing way. Others, myself included, could hardly draw a straight line even with the aid of a drafting machine.
Lettering was a fine art. It's hard to imagine this now, when we select from a thousand fonts with a few mouse clicks, but neat signal names were essential. Some designers used lettering templates. I always found these too cumbersome, and so subjected all readers of my drawings to the same illegible scrawl that the nuns had punished me for in grade school.
Every branch of engineering had its unique set of templates. Digital designers used a handful of plastic stencils that contained the entire stock of resources we worked with: AND and OR gates, inverters and "not" circles, and, of course, various sized squares and rectangles for microprocessors, memories, and everything else. Large chips were rare then; the largest might have a whopping 64 pins, which wasn't too hard to draw.
We drew resistors, capacitors, and other components using similar stencils. With a little practice you could whip the pencil through the zigzag of a resistor template in no time, though a not-perfectly-sharp pencil always resulted in only a hazy image of the part.
Though Luddites scoff that computers let us make mistakes at new, unprecedented rates, in fact even with these crude tools we were quite competently creating errors faster than decent designs. In lieu of a "delete" key we used erasers. Erasers in every form imaginable. In fact, most of us made so many mistakes we used electric erasers, a motorized drill-like device that spun a cylinder of gum-like material. Though these quite effectively removed vast areas of pencil lead, careless use always produced a hole in the vellum. Then what? I suppose mil spec folks started over, recopying the entire drawing onto a fresh sheet of paper. Where I worked we glanced furtively over the shoulder, and rerouted signals around the hole.
Drawings produced by hand - by sloppy electronic folks - had much wider line widths and larger lettering than that we make on computer screens today. As a result the drawings were big. Though some folks used "C" size paper (17 by 22 inches) generally "D" (22 by 34) was the norm. Engineers, production people, and technicians all looked like quintessential architects, with stacks of these monsters on every flat surface. When troubleshooting a new design the first step was to position a big table next to the lab bench - just to hold the drawings.
We drew on vellum, a gauzy semi-transparent material that was pretty tough. It took repeated erasures well, though somehow I always managed to drill a couple of erasing holes through each drawing.
Today we use mostly "A" and "B" sized paper, as that's all laserprinters handle. You can fax or Xerox these drawings without trouble. An ordinary filing cabinet is the perfect storage place. Back then, every business had a "drawing room", dedicated to nothing more than storing (in cabinets called "flat files") and reproducing these huge representations of our tiny circuits. Larger companies had people whose entire role was to file and copy these.
No copier then or now could handle a sheet of D sized paper. One reason we used vellum was its transparency. An engineer duplicating a drawing first put it on top of an equal-size piece of paper coated with a light-sensitive chemical, and ran it through the Ozlid machine. This beast beamed a very intense light through the vellum, exposing areas with no pencil marks. It then treated the paper with ammonia, which turned the unexposed areas blue. The ever-present smell of ammonia (and second hand cigarette smoke!) was simply a part of the engineering environment.
Once the ammonia line broke in the middle of the night. In the morning the entire building was uninhabitable. Fire department fans eventually sucked the fumes out, but we found strange chemical changes in our environment. One secretary's fake flowers changed to a wonderful purple shade. Many pictures hanging on walls now looked like 19th century daguerreotypes. And, of course, several thousand dollars of unused Ozlid paper were completely developed, bright blue reminders of the incident.
Now drawings have no value. Did you spill coffee on a schematic? Just print out a new copy. The information itself if immensely valuable, but its paper incarnation is sacrificial.
Before CAD systems the paper was the only representation of a drawing. The labor required to recreate one was so immense that it was simply inconceivable to lose or mar a schematic. It's funny to realize that one promise of computerization was the paperless office, yet what has happened is paper is now so prevalent that it's worthless. By contrast, in the olden days an original drawing was a holy relic. Copies were scarce because of the cost of duplication and the nuisance of storing the bulky papers.
The regulations said no drawing left the files unless it was being duplicated or was on an engineer's drafting board. Most of us flaunted these rules when the Ozlid machine (which required an hour to warm up) was off at night and we were engaged in a furious troubleshooting war. Living dangerously, with the original by the bench, we'd hope to be done by morning when the drawing Gestapo came in. More than one drawing went back in the files with food stains in the corners.
I suppose it goes without saying that there were no PCB software packages. Either our engineers or outside contractors, leaning over a light table, routed tracks by placing black tape on sheets of mylar. It was a game of chess: the best board designers developed a mental plan of attack which (they hoped) would let them get all of the tracks down without running into dead ends. How things have changed! Now it's great fun to watch the routing program automatically plopping traces down onto the virtual board, at a speed that takes my breath away. In the 70s a big board took weeks, even months, to design.
They routed on mylar, as no paper is dimensionally stable when subjected to humidity variations, and the PCB was made via a photographic reduction of the drawing. My dad, a mechanical engineer from way back, tells me that in the 50s they had the same problem with paper when designing forms for constructing airplanes. Since this predated mylar, they drew on starched linen in ink. Apparently the linen was stable, but it couldn't tolerate water. One drop of sweat dissolved the starch, ruining the drawing. And this was before air conditioning.
It's fascinating to look at things that have not changed with time. Databooks are the best example. I've been convinced for years that CD ROMs, floppy disks, or the net would reduce the engineering library to a single shelf. Yet, we still tromp to the local shows, filling our trunks with a hundred pounds of paper, just as we did in the 70s. There are some rays of light - just the other day I logged into AMD's Web site and downloaded an Acrobat rendition of a datasheet. Now, that was cool - conveniently getting very up-to-date information without dealing with a probably uniformed salesperson.
We learn many skills in life. Some never atrophy. My fingers recalled the compass from two decades past, and guided my son's hand around in a circle. Small ones, big ones; with a bit of practice he was ready to solo. Despite the wonders of computer technology, there's still lots of value in fine motor skills. Kids do art projects to express themselves, but also to develop a mastery of their own fingers.
Me, I'm thankful for modern CAD. I'd never go back to those tedious days of yore.